Why Your Manufacturing Operations Need a Smart Analytics Platform Like ChatGPT
In the age of Industry 4.0, manufacturers face the challenge of making data-driven decisions faster than ever before. With the explosion of Internet of Things (IoT) devices, sensors, and advanced manufacturing systems, there's an immense volume of data generated at every step of production. To truly harness the power of this data, manufacturers need an intelligent analytics platform that can process and provide actionable insights in real-time. This is where smart analytics platforms—similar to ChatGPT—come in.
What is a Smart Analytics Platform for Manufacturing?
A smart analytics platform is a system that integrates with existing manufacturing infrastructure and leverages advanced technologies like Artificial Intelligence (AI), Machine Learning (ML), and IoT to process large amounts of data and provide real-time insights into manufacturing operations. These platforms are designed to monitor, analyze, and optimize every aspect of the manufacturing lifecycle, from production scheduling to quality control, energy consumption, and beyond.
With the rise of Industry 4.0, the importance of such platforms has grown. They are critical in connecting the dots between various systems—like Manufacturing Execution Systems (MES), Enterprise Resource Planning (ERP), and sensors on the factory floor—to drive efficiencies, improve decision-making, and ultimately boost profitability.
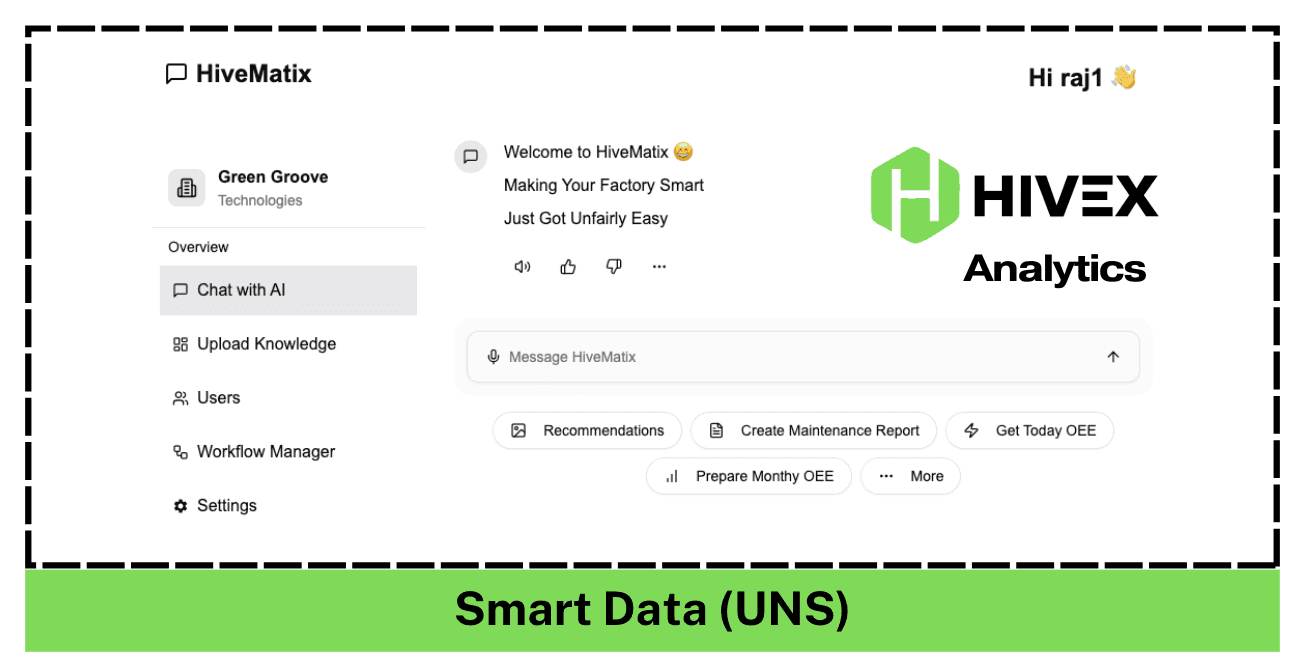
The Extended List of KPIs for Smart Manufacturing
Smart manufacturing requires the ability to track and optimize a wide range of KPIs (Key Performance Indicators). Here’s a look at some of the most important KPIs manufacturers need to track, and how a smart analytics platform can help optimize each:
- Overall Equipment Effectiveness (OEE): Use case: Real-time monitoring of equipment performance using IoT. Benefits: Increased productivity and reduced downtime. OEE helps manufacturers assess how efficiently their equipment is running.
- Cycle Time: Use case: Track and reduce cycle time through process optimization and automated systems. Benefits: Faster production, achieving a 20-30% reduction in cycle time.
- Throughput Rate: Use case: IoT-enabled real-time production monitoring to maximize throughput. Benefits: Improved capacity utilization, increasing output by up to 15%.
- First Pass Yield (FPY): Use case: Automated quality control using AI-powered cameras and sensors. Benefits: Lower defect rates and reduced rework costs.
- Takt Time: Use case: Align production pace with customer demand using real-time scheduling tools. Benefits: Balanced production flow, eliminating bottlenecks.
- Inventory Turnover Ratio: Use case: Real-time inventory management using RFID and IoT. Benefits: Reduced inventory holding costs and optimized stock levels.
- Downtime (Planned vs. Unplanned): Use case: Predictive maintenance using AI to minimize unplanned downtime. Benefits: A potential 50% reduction in unplanned downtime.
- Scrap and Waste Reduction: Use case: Real-time quality monitoring to detect defects early in the process. Benefits: Reduction in material waste by up to 30%.
- Lead Time: Use case: End-to-end visibility of the production process with integrated supply chain systems. Benefits: 25-40% reduction in lead time.
- On-Time Delivery (OTD): Use case: Integrated Advanced Planning and Scheduling (APS) for precise production planning. Benefits: Improved OTD rate, driving customer satisfaction.
- Energy Consumption per Unit: Use case: Energy monitoring using smart meters and IoT sensors. Benefits: Reduced energy costs by 10-15%.
- Cost of Poor Quality (COPQ): Use case: AI-powered defect analysis and real-time quality assurance. Benefits: Lower quality-related costs and higher FPY.
- Labor Productivity: Use case: Human-machine collaboration using cobots and IoT tracking. Benefits: 10-20% increase in productivity.
- Capacity Utilization Rate: Use case: Optimize machine usage through real-time production analytics. Benefits: Improved resource utilization without additional investments.
- Carbon Footprint Reduction: Use case: Real-time tracking of emissions using IoT-based energy management systems. Benefits: Achieve sustainability goals while saving on energy consumption.
How a Smart Analytics Platform Drives Efficiency
A smart analytics platform goes beyond just monitoring data. It provides manufacturers with actionable insights that can drive operational efficiency across various stages of the manufacturing process. Here’s how it can help:
- Real-Time Insights and Analytics: With real-time monitoring, manufacturers can gain instant visibility into their operations. This allows for rapid decision-making to address bottlenecks, reduce downtime, and ensure production goals are being met. Real-time analytics also provide insight into machine health, energy consumption, and even supply chain disruptions.
- Predictive Maintenance: By leveraging AI and machine learning, a smart analytics platform can predict when equipment is likely to fail based on real-time data. This allows for proactive maintenance and helps reduce unplanned downtime, improving overall equipment effectiveness (OEE) by up to 50%.
- Process Optimization: A smart analytics platform provides manufacturers with insights into process inefficiencies, allowing for cycle time reduction, throughput maximization, and improved resource utilization. These optimizations can result in significant savings in both time and costs.
- Quality Control and Waste Reduction: With automated quality control systems powered by AI, manufacturers can detect defects early in the production process, reducing waste and improving the first-pass yield (FPY). Real-time quality assurance also lowers rework costs and ensures that only high-quality products make it to the final stages.
- Sustainability Monitoring: Sustainability is a key driver in modern manufacturing, and smart analytics platforms help manufacturers track and reduce their environmental impact. From energy consumption to carbon emissions, these platforms provide the tools to monitor and optimize processes to meet sustainability goals and save on energy costs.
How We Enable Smart Analytics in Manufacturing
At Green Groove, we’ve developed an advanced analytics platform that is specifically designed to empower manufacturers in their Industry 4.0 journey. Our platform integrates seamlessly with your existing manufacturing infrastructure, pulling data from IoT sensors, ERP systems, MES, and other sources to provide a centralized hub for real-time insights.
We leverage the power of AI, Machine Learning, and data analytics to give manufacturers the tools they need to track and optimize KPIs in real-time. From predictive maintenance and quality control to energy optimization and sustainability monitoring, our platform drives both operational and financial efficiencies.
The Benefits of Smart Analytics for Manufacturers
- Improved Operational Efficiency: By tracking real-time data, manufacturers can make informed decisions to improve throughput, reduce cycle times, and maximize equipment utilization.
- Cost Reduction: A smart analytics platform helps reduce waste, downtime, and energy consumption, resulting in significant cost savings.
- Enhanced Product Quality: With automated quality control and real-time defect detection, manufacturers can improve their first-pass yield, reduce scrap rates, and enhance product quality.
- Better Decision-Making: The ability to make data-driven decisions ensures that managers can optimize production schedules, resource allocation, and production workflows.
- Sustainability and Compliance: Monitoring energy usage and emissions helps manufacturers meet sustainability goals while optimizing costs.
- Scalability: Smart analytics platforms can grow with your business, providing flexibility to adapt to new challenges and opportunities in the manufacturing process.
Conclusion
The future of manufacturing is here, and it’s powered by data. As the industry evolves towards Industry 4.0, manufacturers need an intelligent platform that can turn raw data into valuable insights. A smart analytics platform provides just that—enabling real-time monitoring, predictive maintenance, process optimization, and quality control.
At Green Groove, we’ve developed a cutting-edge platform that empowers manufacturers to harness the full potential of their operations. By leveraging IoT, AI, and real-time analytics, we’re helping manufacturers boost productivity, reduce costs, improve quality, and meet sustainability goals.
Ready to take your manufacturing operations to the next level? It’s time to embrace smart analytics and unlock the full potential of your production processes with Green Groove’s platform.